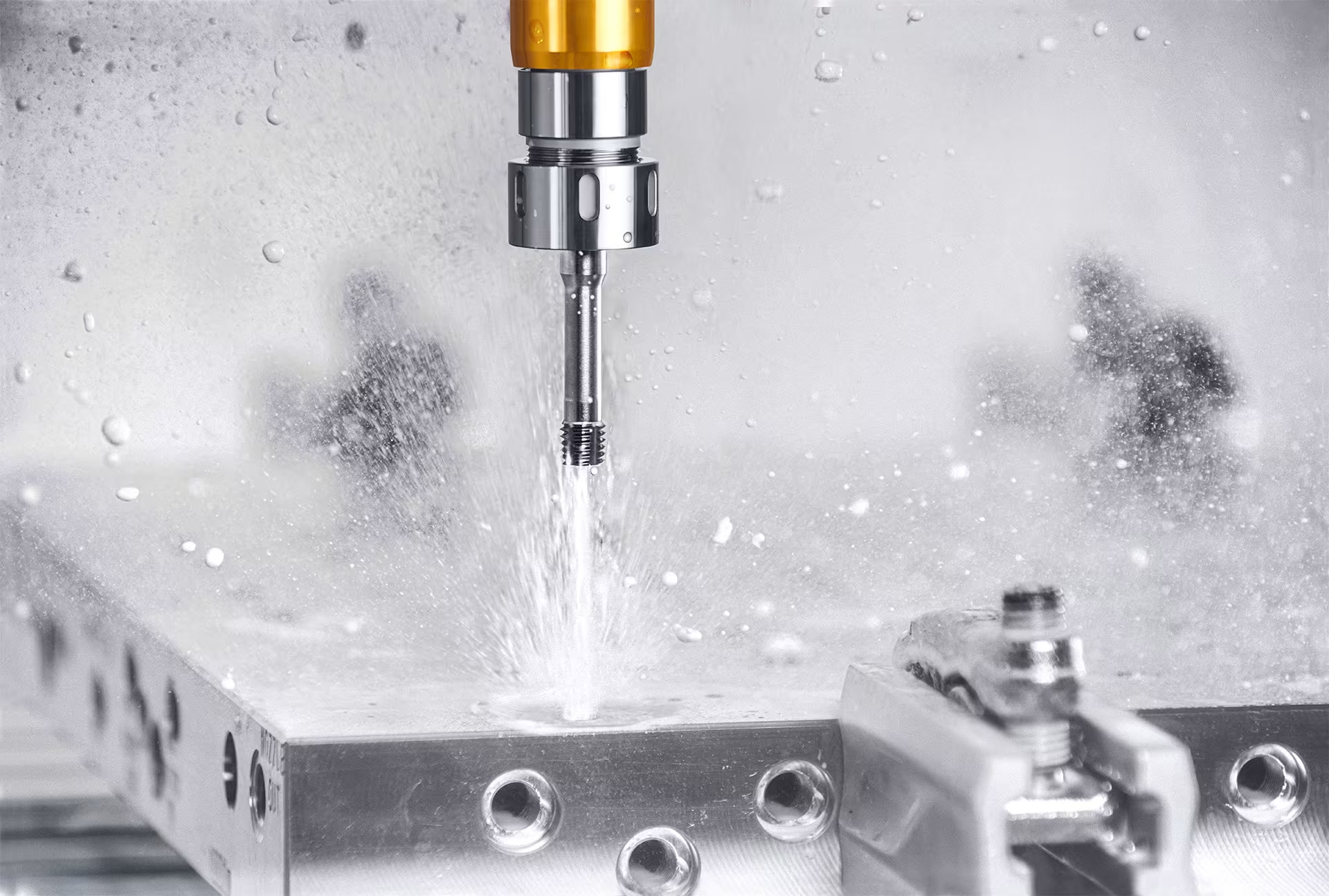
Anwenderreportage MAPLAN Systems GmbH
HPF Max Former
Effiziente Gewindebearbeitung mit dem modularen HPF Max Former: Optimierte Bearbeitungszeiten bei der MAPLAN Systems GmbH in Villingen-Schwenningen
Ein Großprojekt der MAPLAN Systems GmbH forderte die Fertigung gleich mehrerer komplexer Bauteile mit einer hohen Anzahl an Gewinden in Stahl im Werkstoff 1.2312 – eine hohe Präzision und absolute Prozesssicherheit galten als unerlässlich. Wie MAPLAN diese Herausforderungen im Formenbau mit dem HPF Max Former der LMT Tools bewältigt hat, zeigt ein Blick hinter die Kulissen.
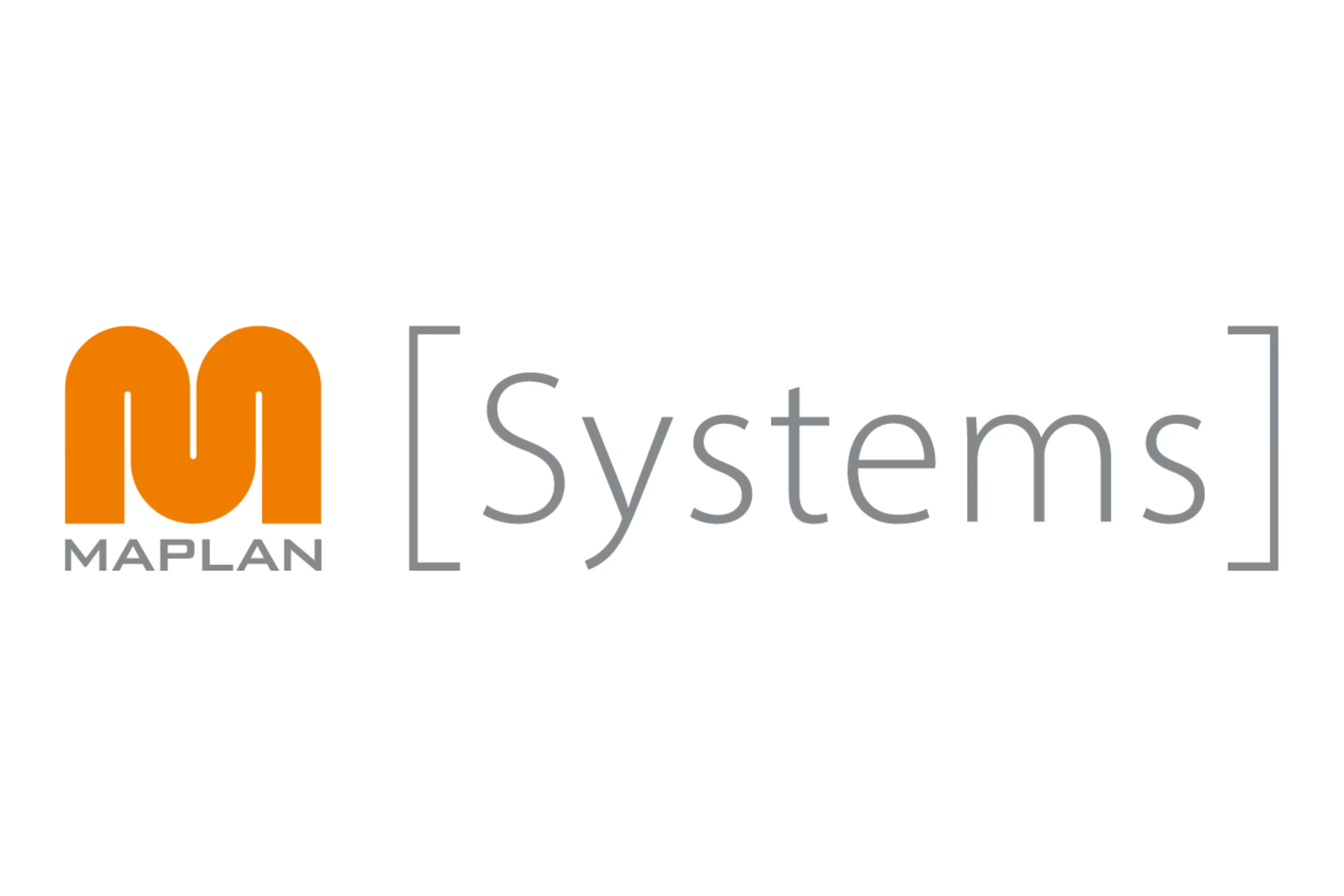
Der Anwender im Porträt
MAPLAN ist führender Hersteller von Elastomer-Spritzgießmaschinen und bietet umfassende 360° Systemlösungen für die halb- und vollautomatische Produktion von Gummi- und Silikonprodukten. Als Komplettanbieter liefert das Unternehmen Maschinen, Kaltkanäle, Werkzeuge und schlüsselfertige Automatisierungs-Anlagen für Kunden aus Automotive, Bahnindustrie, Energietechnik, Medizintechnik sowie Haushaltsgeräteindustrie.
Neben dem Hauptsitz in Österreich und Niederlassungen in den USA, China, Indien, Deutschland, Frankreich, Italien, Slowakei ist MAPLAN mit mehr als 20 weltweiten Vertriebs- und Servicestandorten global vertreten.
Dabei bildet die MAPLAN Systems GmbH, im Süden Deutschlands, das Kompetenzzentrum für die Fertigung von präzisen Werkzeugen und Kaltkanälen.
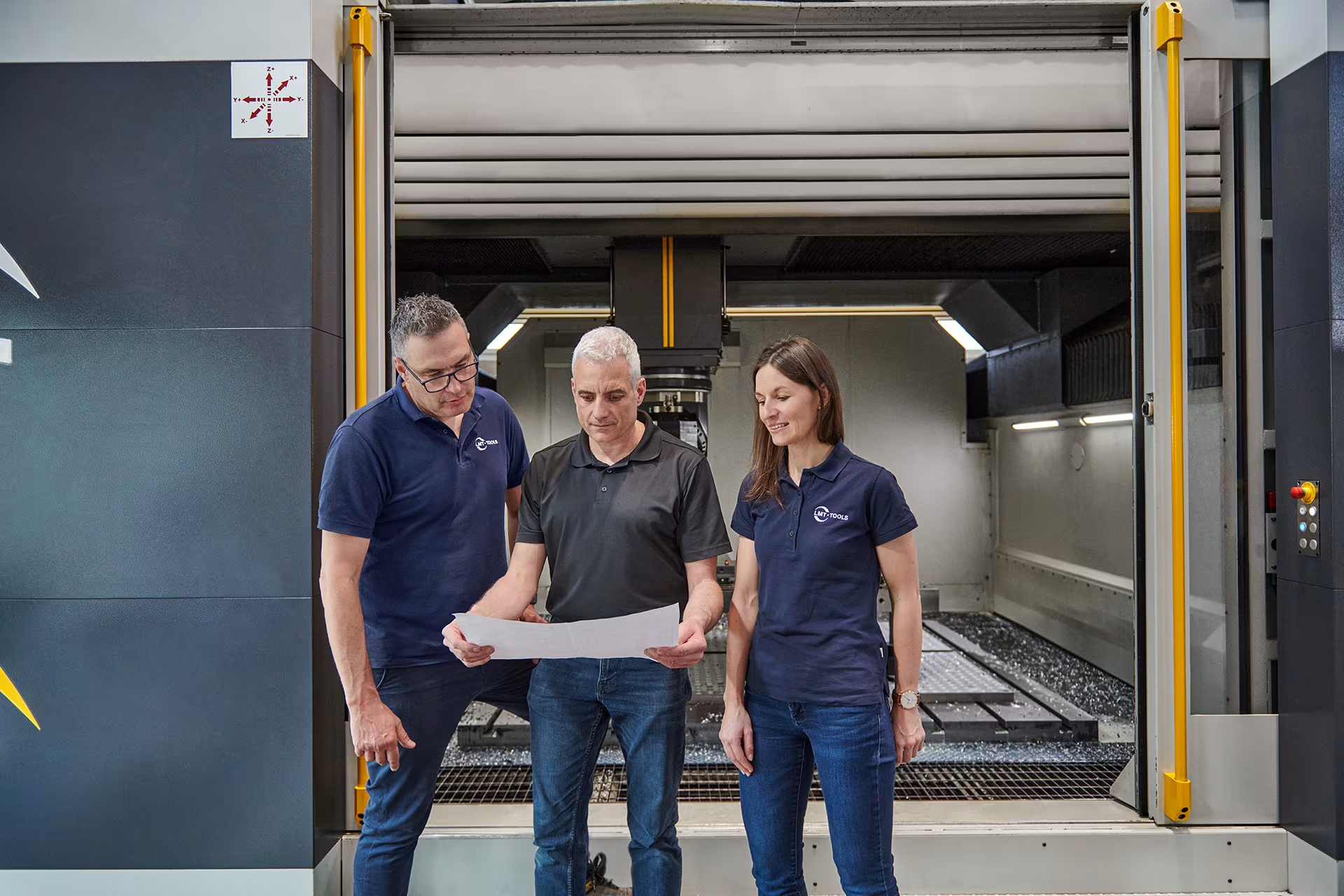
Ausgangssituation: Hohe Anforderungen an Präzision und Prozesssicherheit im Formenbau
Die MAPLAN Systems GmbH in Villingen-Schwenningen ist spezialisiert auf anspruchsvolle Einzelteilfertigung im Formenbau. Bei einem aktuellen Projekt sollten mehrere Bauteile mit einer hohen Anzahl an Gewinden in Stahl, im Werkstoff 1.2312 gefertigt werden – jeweils mit hoher Präzision und absoluter Prozesssicherheit. Da es sich um die finale Bearbeitungsstufe der Werkstücke handelte, war ein fehlerfreier und stabiler Prozess entscheidend. Gleichzeitig galt es, die Bearbeitungszeiten zu optimieren und eine wirtschaftliche Umsetzung in der Einzelteilfertigung sicherzustellen.
Für diese Herausforderungen suchte MAPLAN einen zuverlässigen Partner mit umfassender Gewindekompetenz – und fand ihn in LMT Tools. Mit dem modularen HPF Max Former der Marke LMT Fette konnte eine Lösung implementiert werden, die sowohl die geforderten Qualitätsstandards erfüllte als auch die Effizienz der Fertigung deutlich steigerte.
Welche Vorteile sah Ralph Hug von MAPLAN Systems GmbH in dem Gewindeformen und der Umsetzung mit dem Modularen HPF Max Former?
Da es sich beim Gewindeschneiden um den letzten Bearbeitungsschritt im Fertigungsprozess handelt, war die Prozesssicherheit für Ralph Hug, Betriebsleiter bei MAPLAN Systems GmbH, von zentraler Bedeutung. Die Wahl fiel bewusst auf das spanlose Verfahren des Gewindeformens.
„Ich habe mit LMT Kieninger im Gesenk- und Formenbau sehr gute Erfahrungen gemacht – sowohl hinsichtlich Qualität und Leistungsfähigkeit der Werkzeuge als auch beim Service“, erklärt Hug. „Für diesen Auftrag mit wiederkehrenden Gewinden war es mir wichtig, einen zuverlässigen Partner mit umfassender Gewindekompetenz an der Seite zu haben. Deshalb fiel meine Entscheidung auf LMT Fette.“
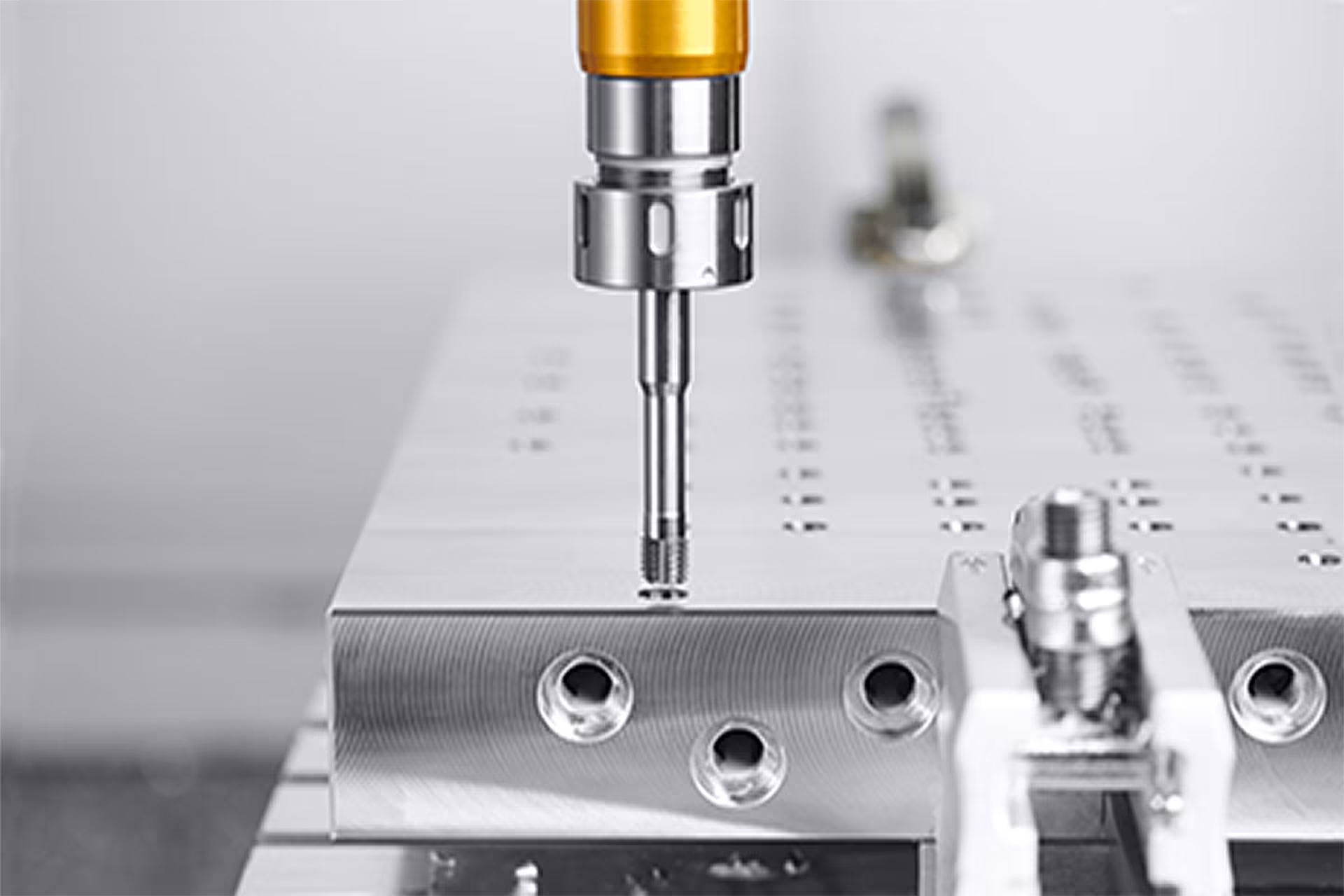
Die optimale Werkzeug-Lösung: Der modulare Gewindeformer HPF Max
Der modulare HPF Max Former von LMT Tools kombiniert die Verschleißfestigkeit eines Hartmetall-Gewindekopfes mit der Zähigkeit eines Stahlschafts – ideal für anspruchsvolle Gewindeapplikationen. Durch seine hohe Umfangsgeschwindigkeit verkürzt er die Bearbeitungszeit signifikant.
Ein weiterer Pluspunkt: Mit nur einem Werkzeughalter lassen sich unterschiedliche Gewindeabmessungen realisieren. Das reduziert sowohl die Rüst- als auch die Werkzeugkosten erheblich. Neben dem umfangreichen Standardprogramm bietet LMT Tools zudem kundenspezifische Sonderlösungen, individuell abgestimmt auf die jeweilige Anwendung.
Das Ergebnis? Eine deutliche Effizienzsteigerung und reduzierte Fertigungskosten
Mit dem Einsatz des modularen HPF Max Formers konnte MAPLAN Systems GmbH nicht nur die Bearbeitungszeiten reduzieren, sondern auch eine hohe Prozesssicherheit und eine stabile Serienproduktion sicherstellen – sogar im mannlosen Betrieb.
Das Fazit: Präzision und Wirtschaftlichkeit vereint
Die Implementierung des HPF Max bei MAPLAN Systems GmbH unterstreicht die Bedeutung der richtigen Werkzeugwahl für eine stabile, wirtschaftliche und automatisierte Gewindefertigung.
„Mit dem modularen Former HPF Max von LMT Tools konnten wir unsere Fertigung deutlich effizienter gestalten und gleichzeitig die Standzeiten der Werkzeuge erhöhen.“ – Ralph Hug, Betriebsleiter, MAPLAN Systems GmbH
Dieses Projekt zeigt: Mit dem richtigen Werkzeug lassen sich auch anspruchsvollste Fertigungsaufgaben sicher und wirtschaftlich lösen. Wir danken MAPLAN Systems GmbH für das Vertrauen und freuen uns auf weitere erfolgreiche Projekte in der Zukunft.
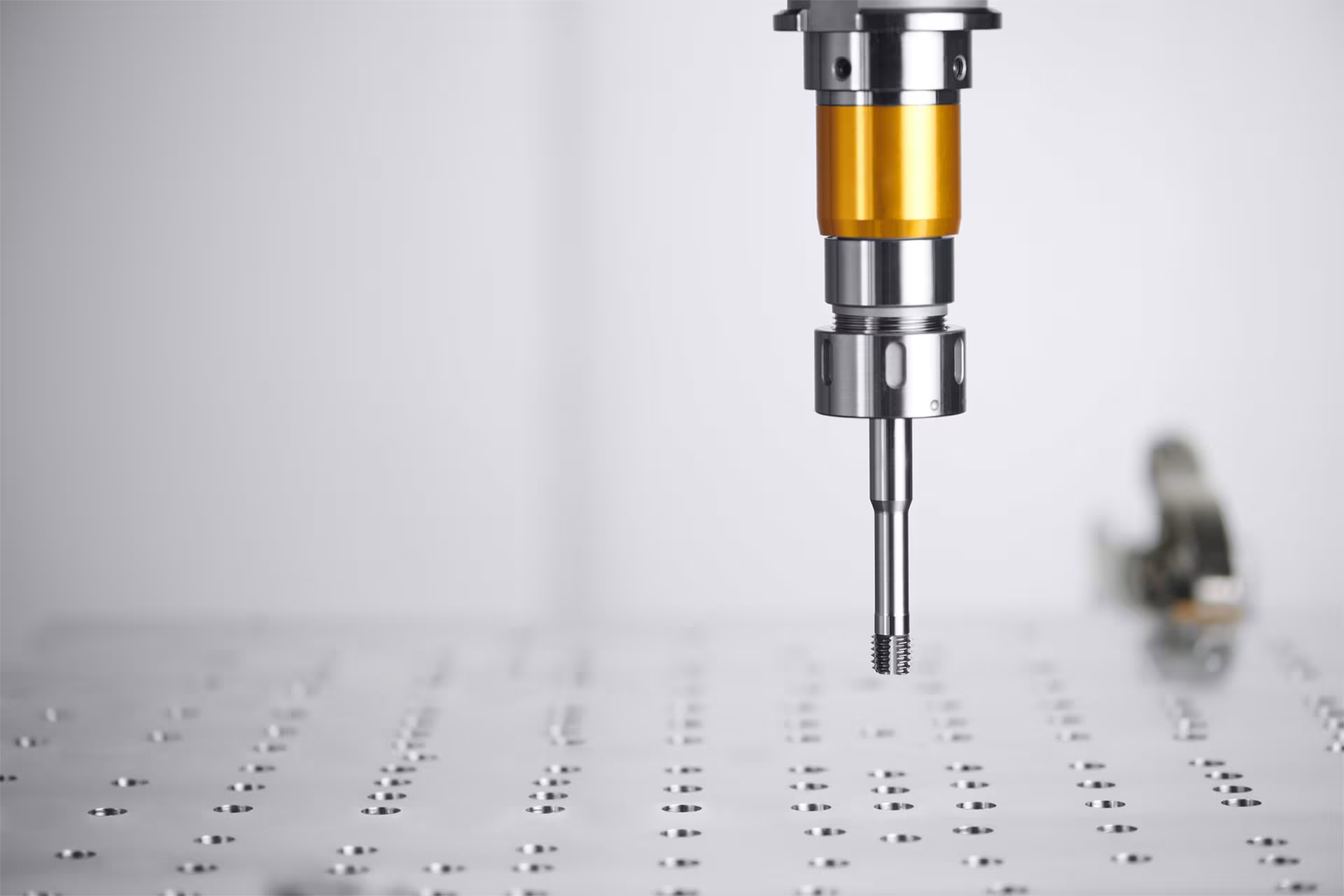
Möchten auch Sie Ihre Prozesse optimieren?
Kontaktieren Sie unser Team für eine individuelle Beratung unter info@lmt-tools.com oder entdecken Sie den HPF Max direkt im Shop:
zum Shop