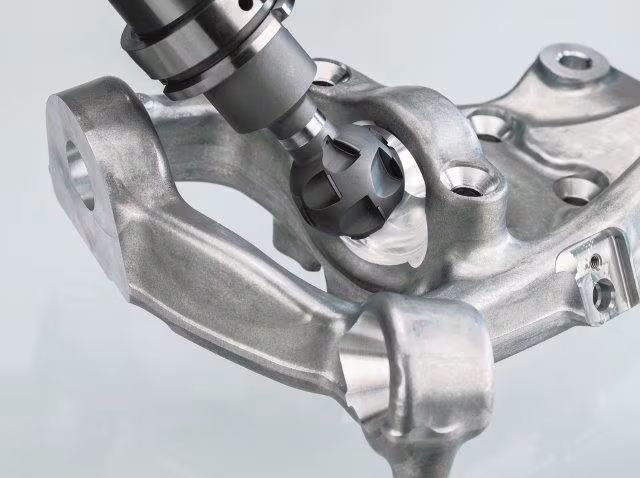
Advanced Tools
Complete Solutions Customized for You
Your Innovative Technology Partner
With our Advanced Tools, we go – together with you – above and beyond the design and deployment of individual tools. The idea: Use us as your strategic technology partner for the development of complete machining strategies (“project engineering”) and extremely precise tool systems. Our central focus: To strengthen your productivity and – especially in large-series production – to reduce the cost per unit (CpU).
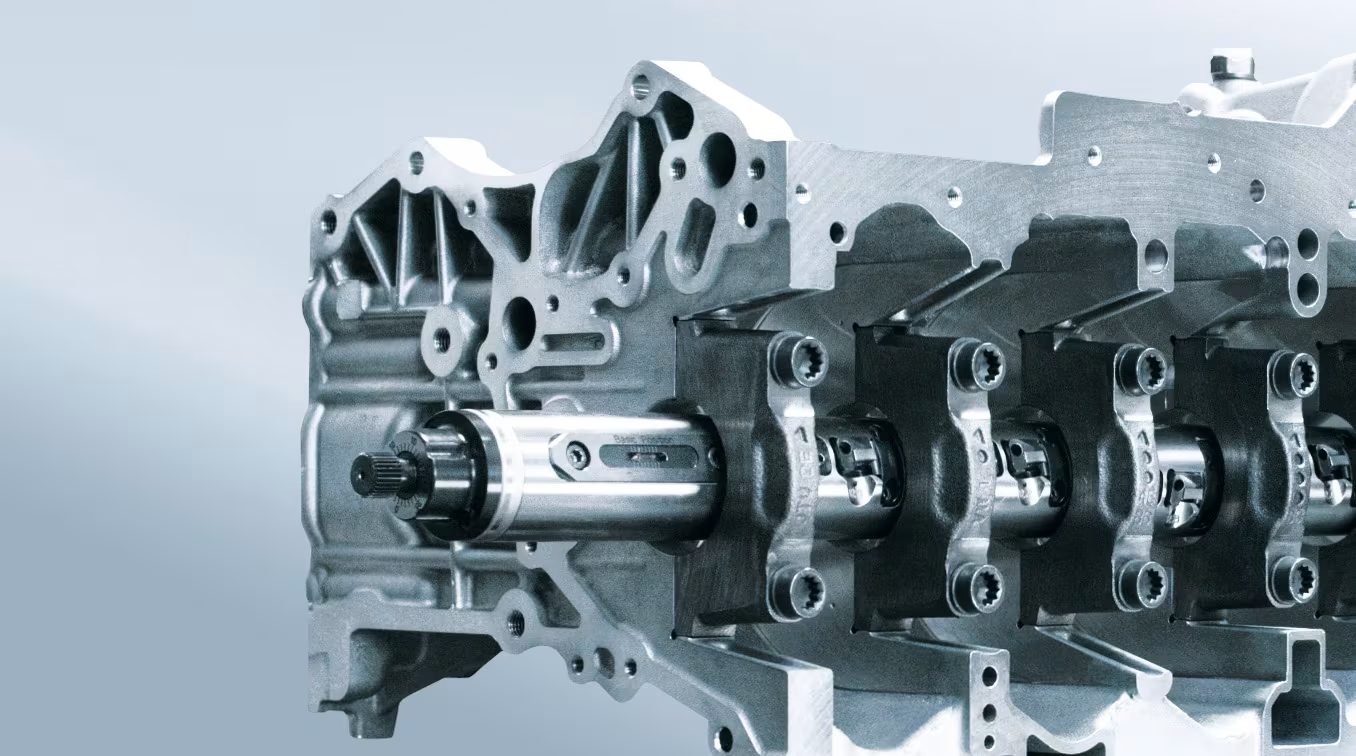
Automatically Adjustable Tools
Control tools for machining crankshaft bearing bores are used with maximum precision and efficiency. These tools function like an actuator. The diameter of the inserts can be adjusted via an internal tie rod, e.g. to compensate for wear.
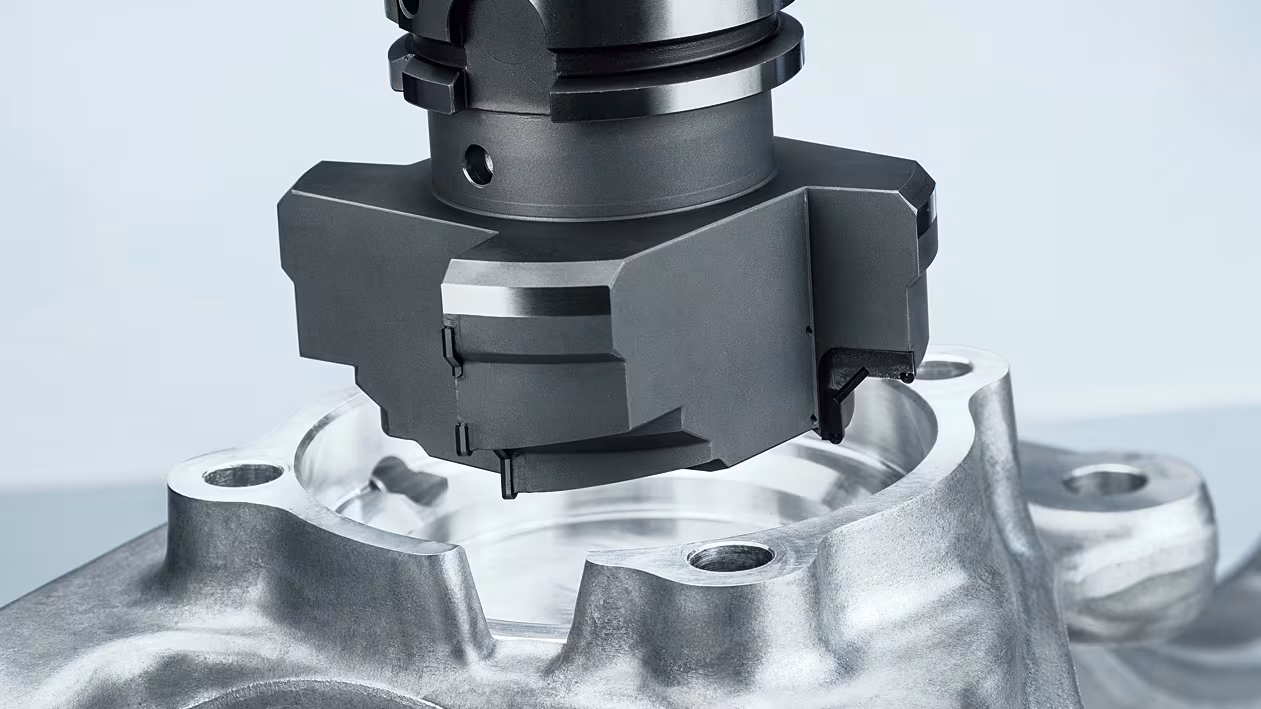
PCD Tools
Tools with PCD cutting materials guarantee maximum performance when machining engine components and aluminum housing units. Multi-step PCD tools not only achieve absolute precision in the machining process, but also positively influence the costs of the complete process.
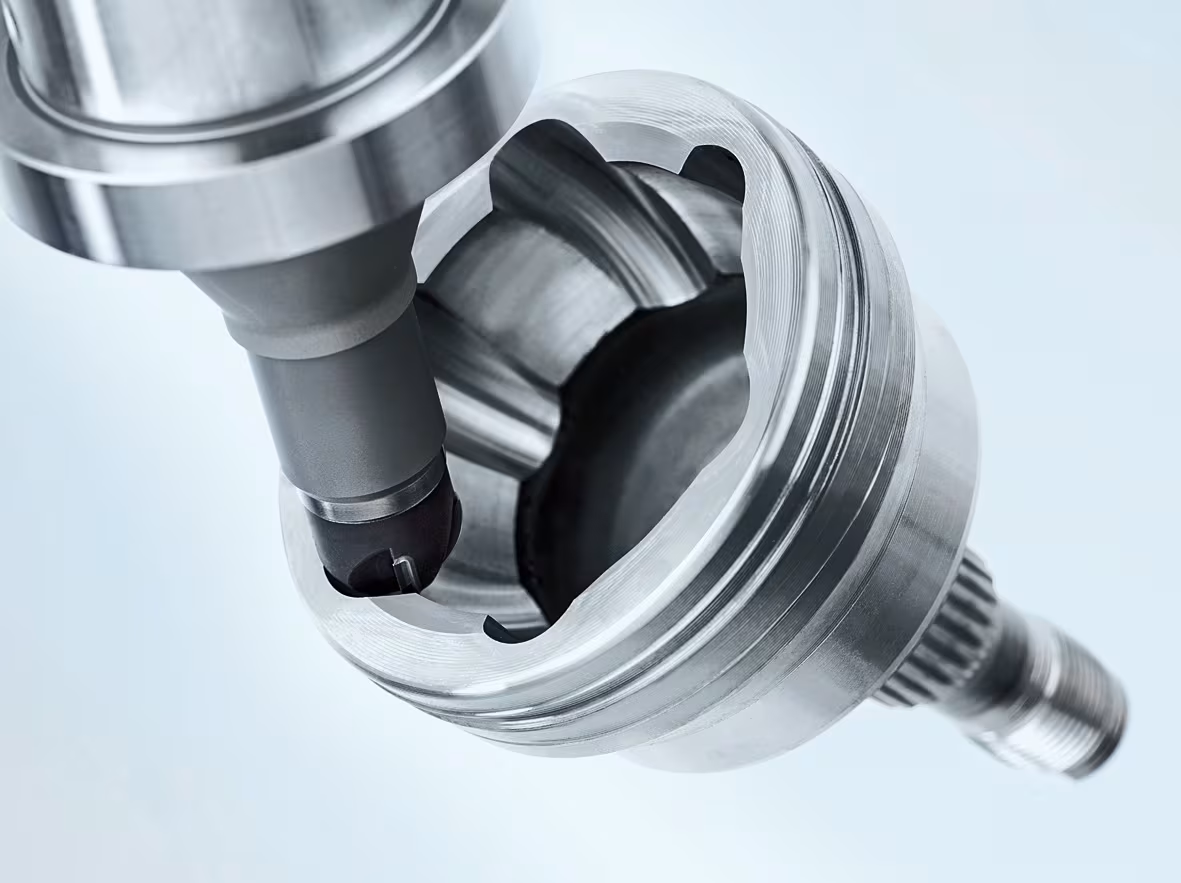
CV Joint Tools
The machining of joints places high demands on the quality of precision tools when it comes to shape accuracy and tool life. This is true for the soft milling sector using coated carbide tools, as well as for the hard milling of induction-hardened components using CBN cutting materials.
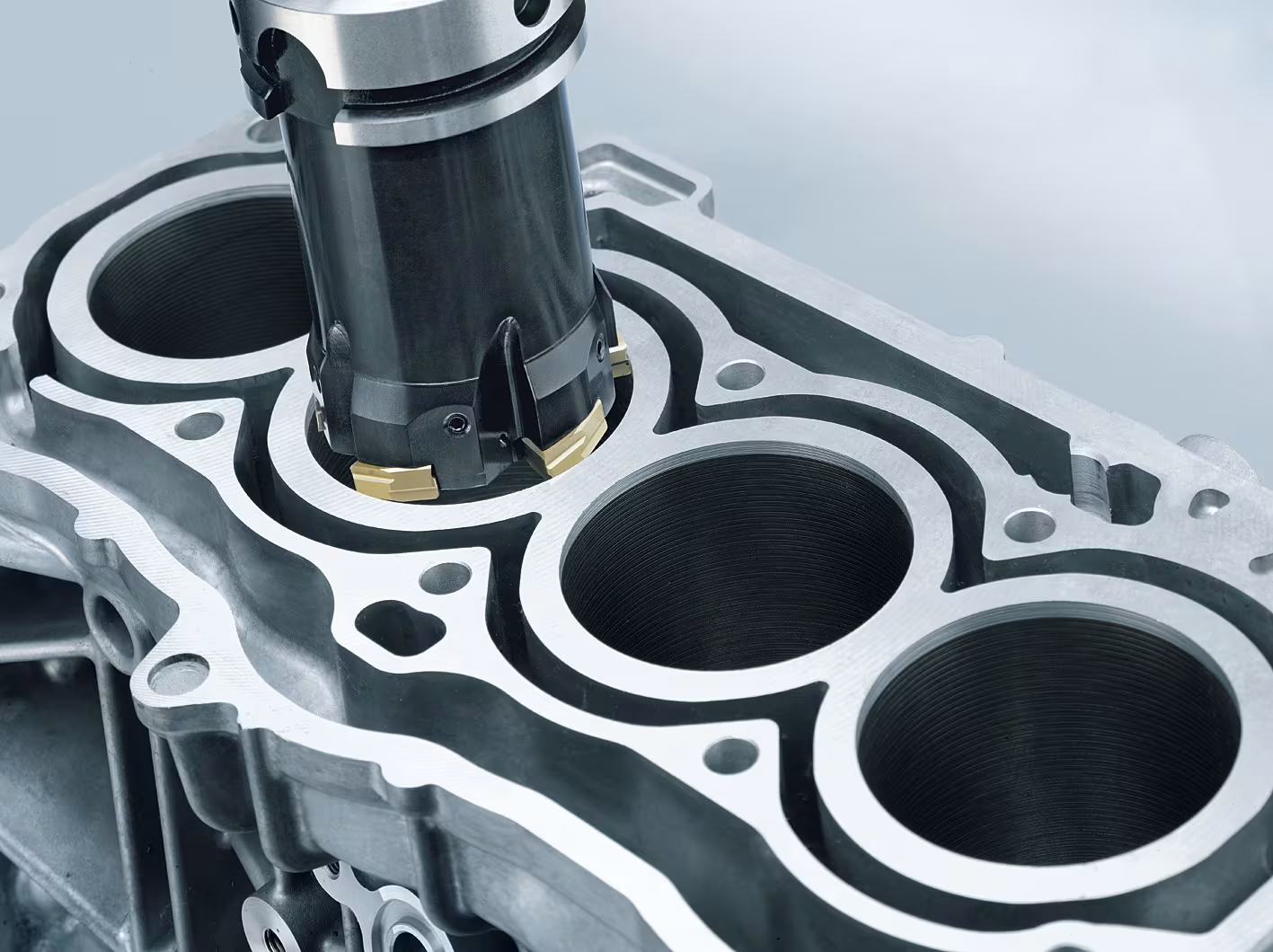
Tangential Indexable Inserts
Tangential technology opens up new possibilities for tool conception and construction, promising maximum performance in the machining process. With tangential technologies, the cutting strengths are absorbed over the entire plate profile, thereby significantly prolonging tool life.
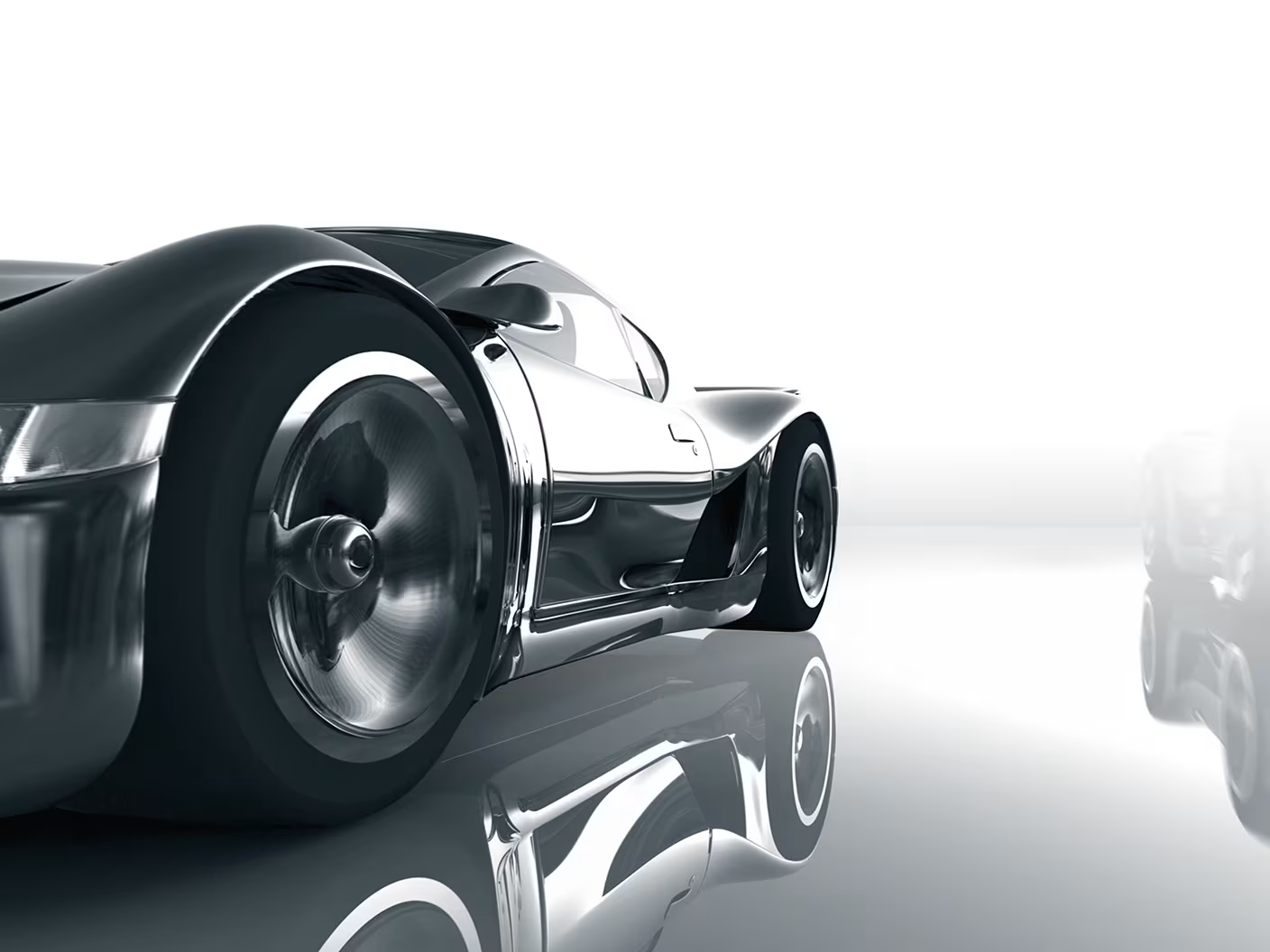
Tool Solutions That Will Change Technology
Lightweight construction, downsizing, alternative drives – there is hardly another industry facing similar challenges to the automotive sector. As a result, the production process is continuously changing as well. Precision tools play an important role in this context.
Do you have any questions about us or our products? Please do not hesitate to contact us!
We would be happy to provide you with more information. Together, we develop solutions to make your production more efficient, innovative, and future-focused.
Just give us a call or contact us directly via contact form. For product details and orders, please use our online shop or our catalog as well.