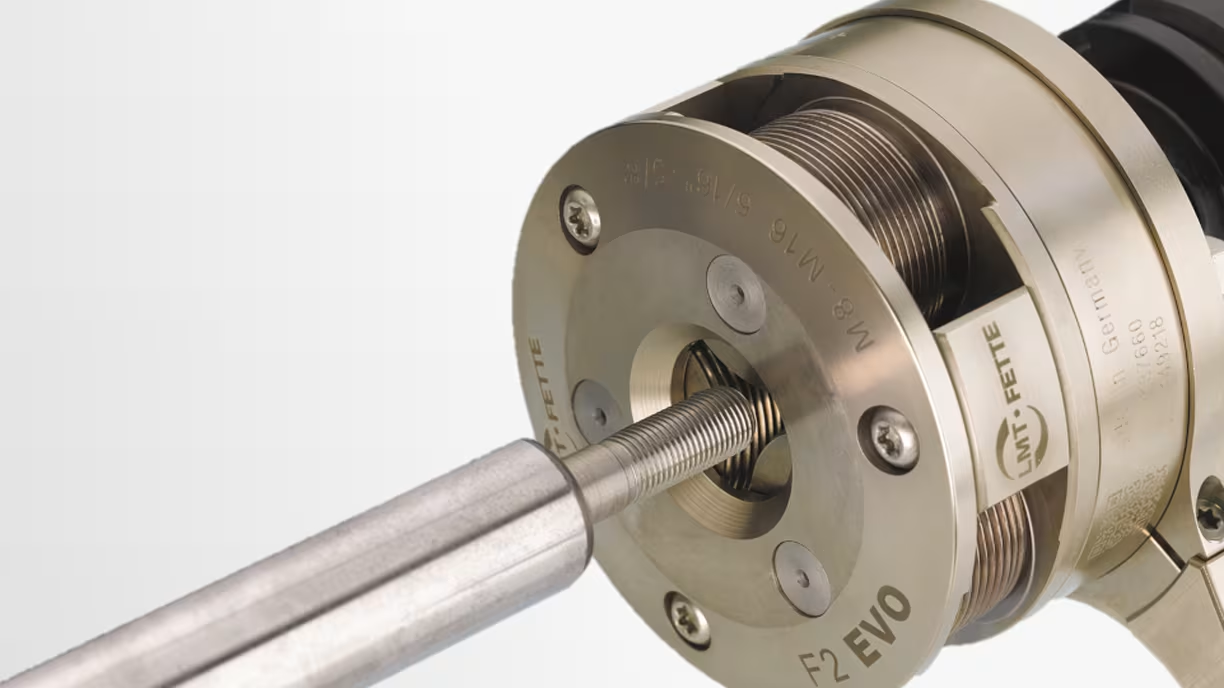
Thread Rolling and Rollable Profiles
Possible Applications for Rolling Heads: Thread Rolling and Production of External Profiles
Rolling heads can be used on almost all processing machines in a wide variety of positions. Depending on the design, they can be mounted on lbasic engine lathes, pillar drills, single and multiple spinde bar and chucking machines, rotary transfer machines, NC and CNC lathes, machining centers, drill presses, special purpose machines and moving head stock lathes. The use of a thread rolling head also offers decisive advantages on NC and CNC machines: The thread is completed in a single pass in seconds, while CNC-controlled cutting or chasing, on the other hand, usually requires several passes. This saves expensive machine time.
LMT Fette offers a variety of thread rolling head designs, e.g. for all common thread types in the diameter range 1.4 mm to 230 mm. But our solutions also make it possible to manufacture numerous special and custom profiles in almost all materials.
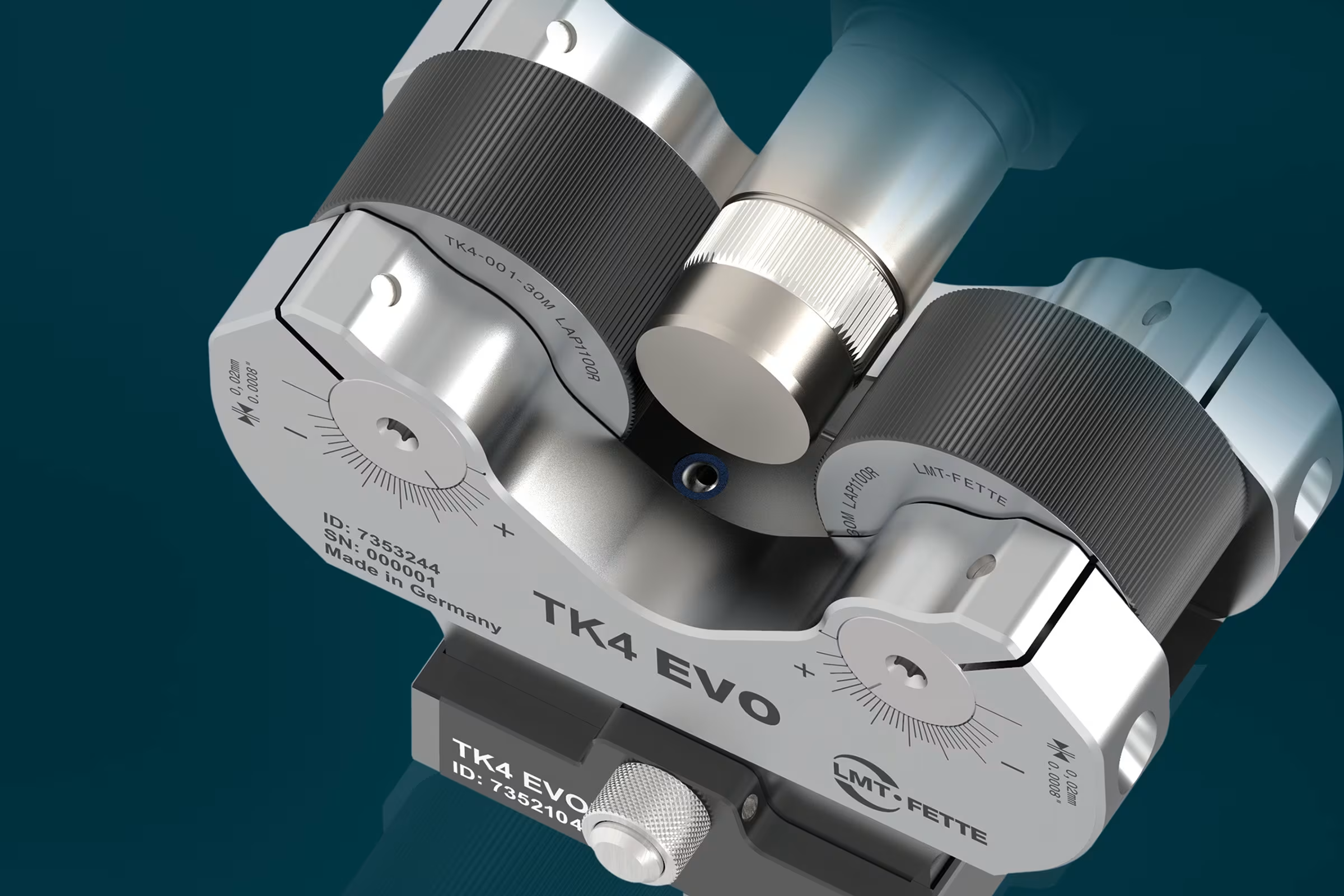
Advantages of Cold Forming Threading
- Enormous achievable material removal rates enable cost savings through cycle time reduction
- Very economical
- Short production times
- Extremely long tool life
- Increased thread strength
- High surface finishing
- Consistent repeatable accuracy
- Improved machine utilization ...and additional advantage: No chips are produced!
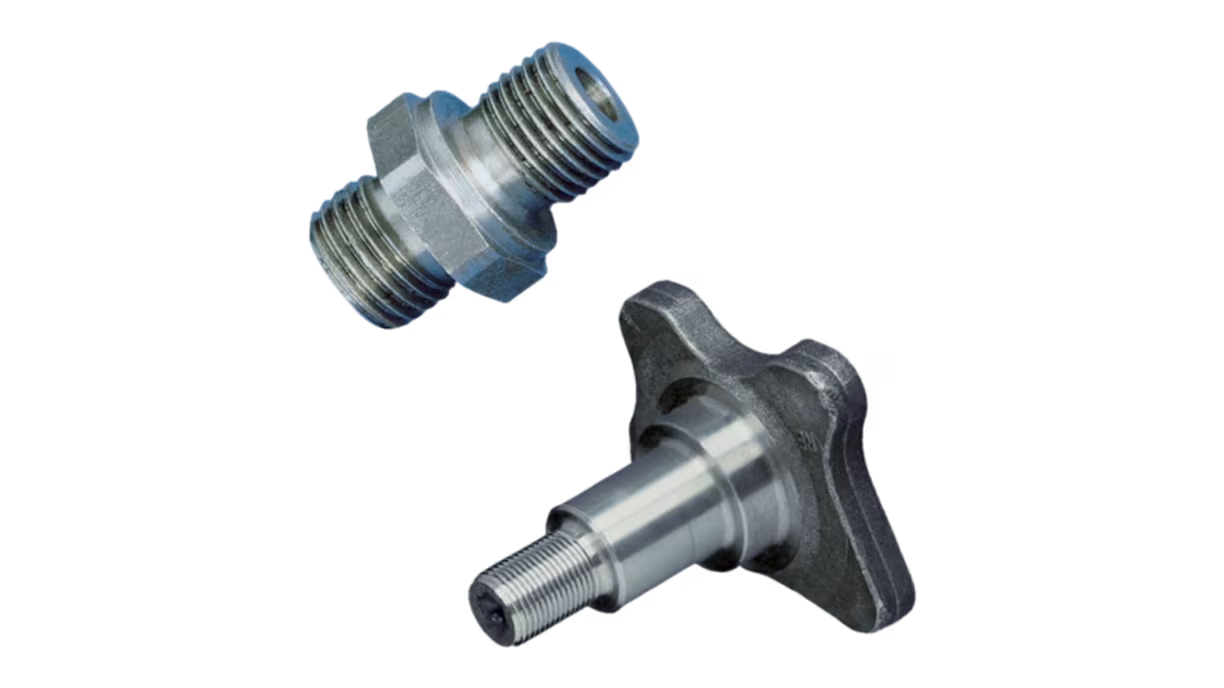
Thread Rolling in the Front and Behind the Shoulder
Almost all standardized threads such as parallel and tapered “V” threads, knuckle and half knuckle threads, parallel type wood screw threads and in certain circumstances even buttress threads can be rolled by using a thread rolling head. Flank angle should not be less than 20°. Within this range of conditions any special shaped thread can be rolled. Diameters may be rolled between 1.4 mm to approx. 230 mm (0,055” to approx. 9,055“).
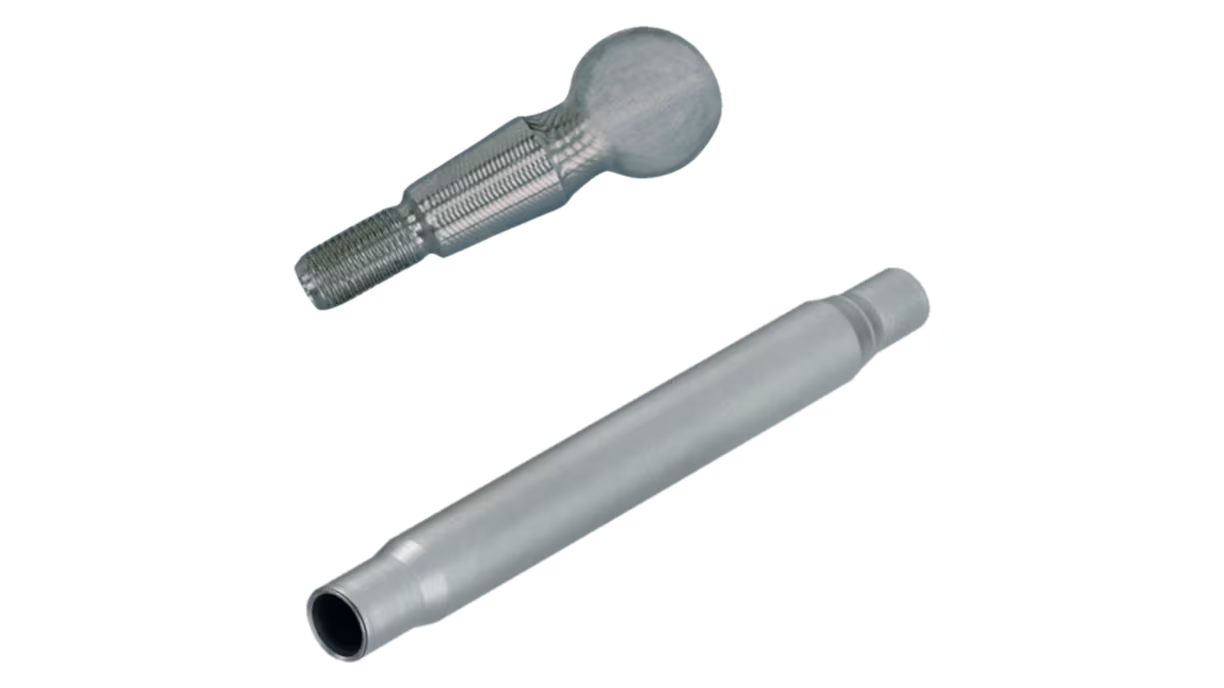
Sphere Burnishing and Swaging of Tubes
Surfaces of cylindrical components can be burnished with burnishing rolls and pipe ends can be reduced, beveled or swaged with profiled rolls. In principle, thread rolling on tubular parts, such as pipes, is possible in many cases. With thin-walled pipe parts, the inner wall is supported by an inserted arbor. However, the remaining wall thickness between the diameter of the thread core and the inner diameter of the pipe should not be less than 0.5 mm + half the thread depth.
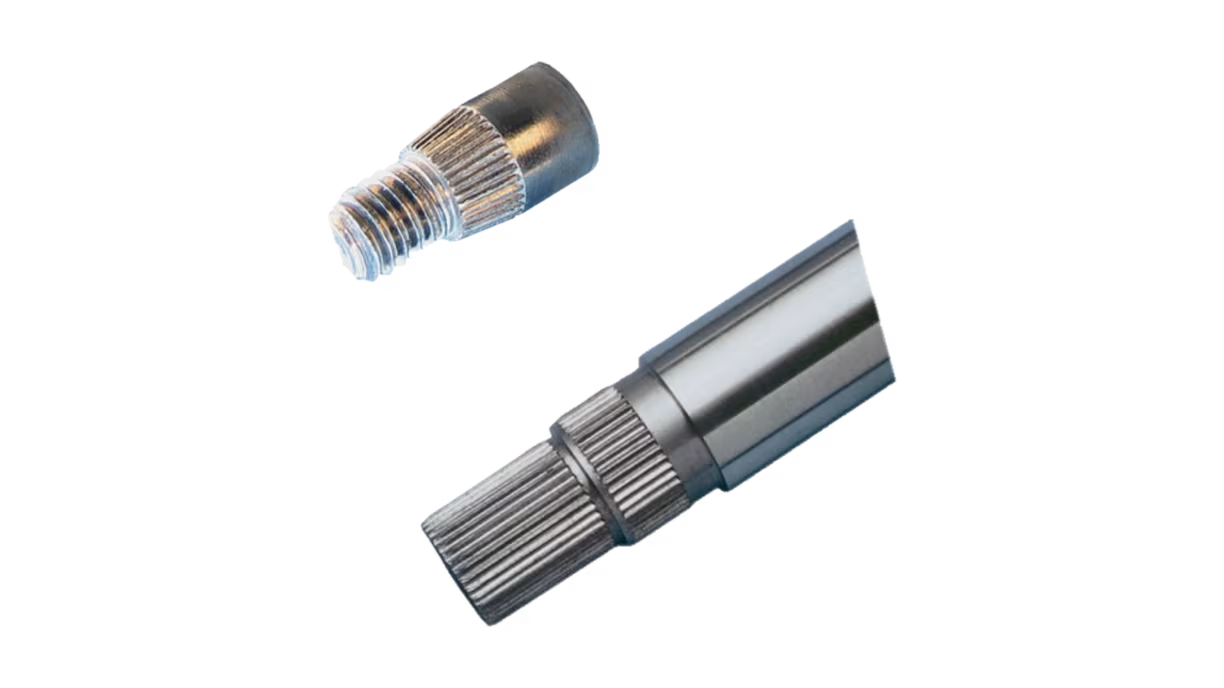
Knurls And Spline Serrations
In addition to the production of external threads, LMT Fette rolling heads are also suitable in many cases for knurling, burnishing surfaces and beading. LMT Fette rolling heads can also be used to produce serrations with a gap angle of about 90°. In order to be able to provide workpieces with the required number of teeth, a master pinion is installed with axial spring action between the rolls.
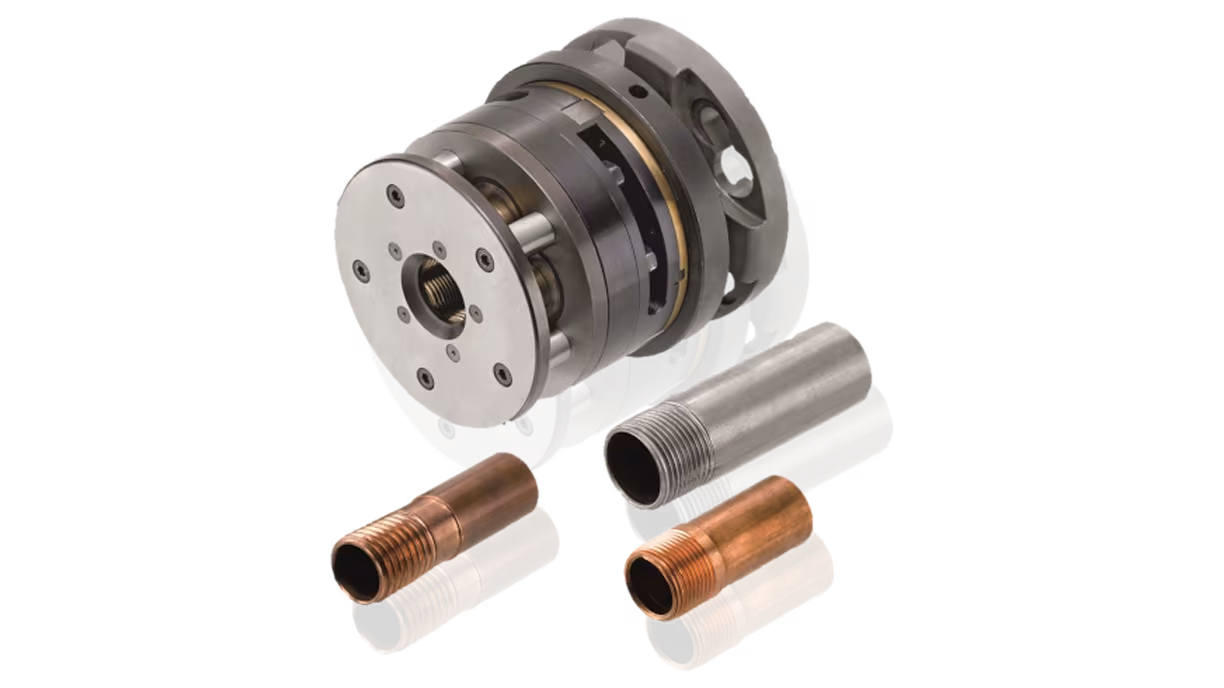
Rollability of Materials
In general, the materials to be processed with a rolling head should have a minimum elongation of about 7% and not exceed a tensile strength of 1700 N/mm² (246560 PSI) to ensure rollability. Rollable materials include construction and case-hardened steel, stainless steel, quenched and tempered steel up to about 1600 N/mm², as well as white brass, copper, light metals and ferritic cast grades such as GGG40 or GTS35. Brittle materials with low elongation such as cast iron, hard brass alloys and hardened materials are not suitable for thread rolling.
The table below is suitable for a simple determination of the rollability of materials. The data should be regarded as guide values which, however, may vary depending on machine conditions, microstructure and rolling head type. For precise technical clarification, we therefore generally recommend consulting our customer service.
Thread rolling heads and rolling systems:
Our expertise to your advantage
We would be happy to provide you with more information. In addition to our comprehensive program and the quality of our products, the services related to the use of our products also belong our strengths. Our application technicians are happy to provide consultation on the optimized use of our rolling systems – on location and practice-oriented. At out LMT Tools Training Center we demonstrate the latest thread tool technology. At out Test Center we perform tests for you - on your workpieces - to optimize the application and the processes. Our technical seminars provide you with comprehensive theoretical and practical knowledge.
If you have any technical inquiries, please contact our team Rolling Systems directly:
T: +49 4151 12391
You can also use our general contact form for commercial inquiries: