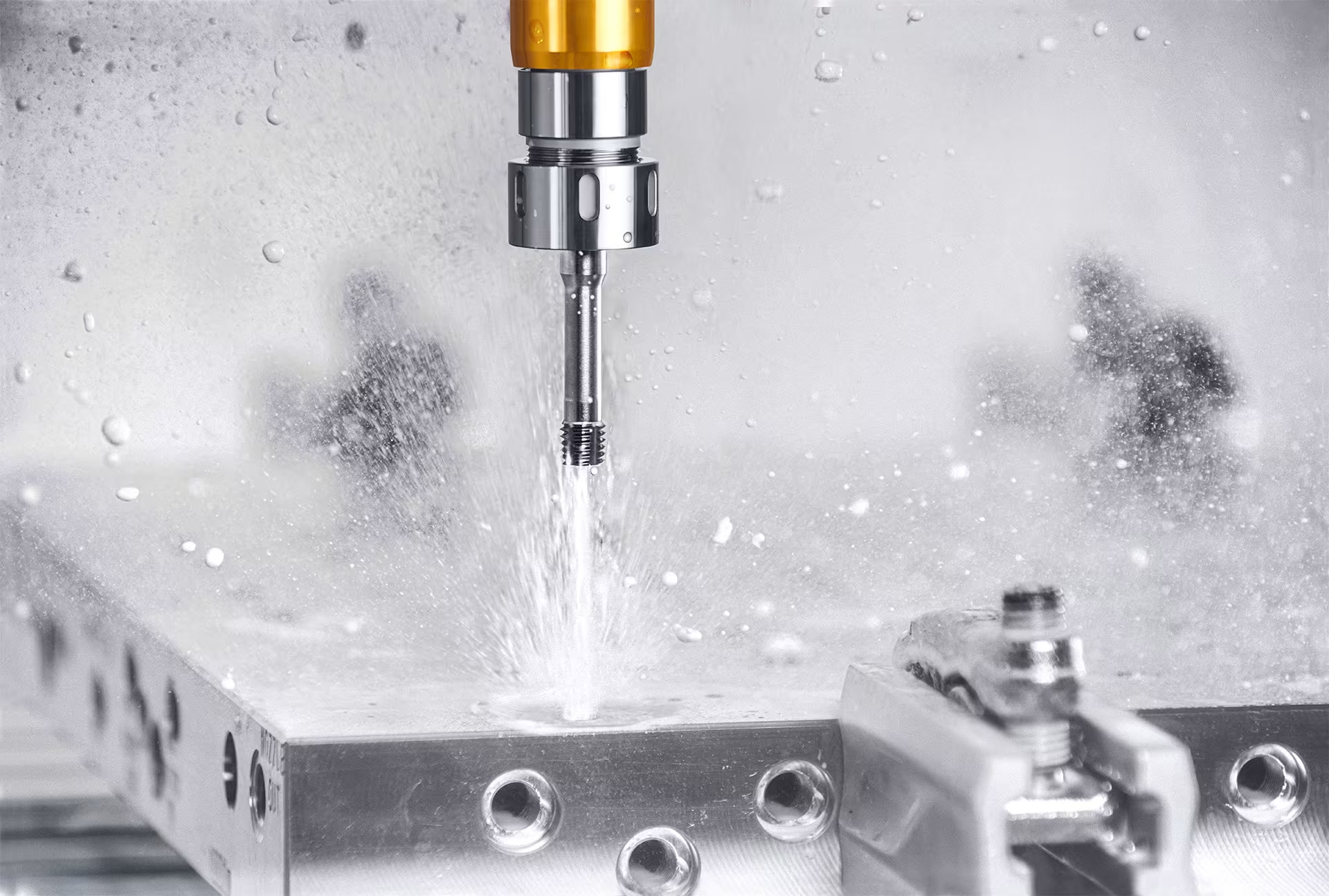
User Report MAPLAN Systems GmbH
HPF Max Former
Efficient thread machining with the modular HPF Max Former: Optimized machining times at MAPLAN Systems GmbH in Villingen-Schwenningen
A major project at MAPLAN Systems GmbH required the production of several complex components with a large number of threads in steel in the material 1.2312 - high precision and absolute process reliability were essential. A look behind the scenes shows how MAPLAN overcame these challenges in mold making with the HPF Max Former from LMT Tools.
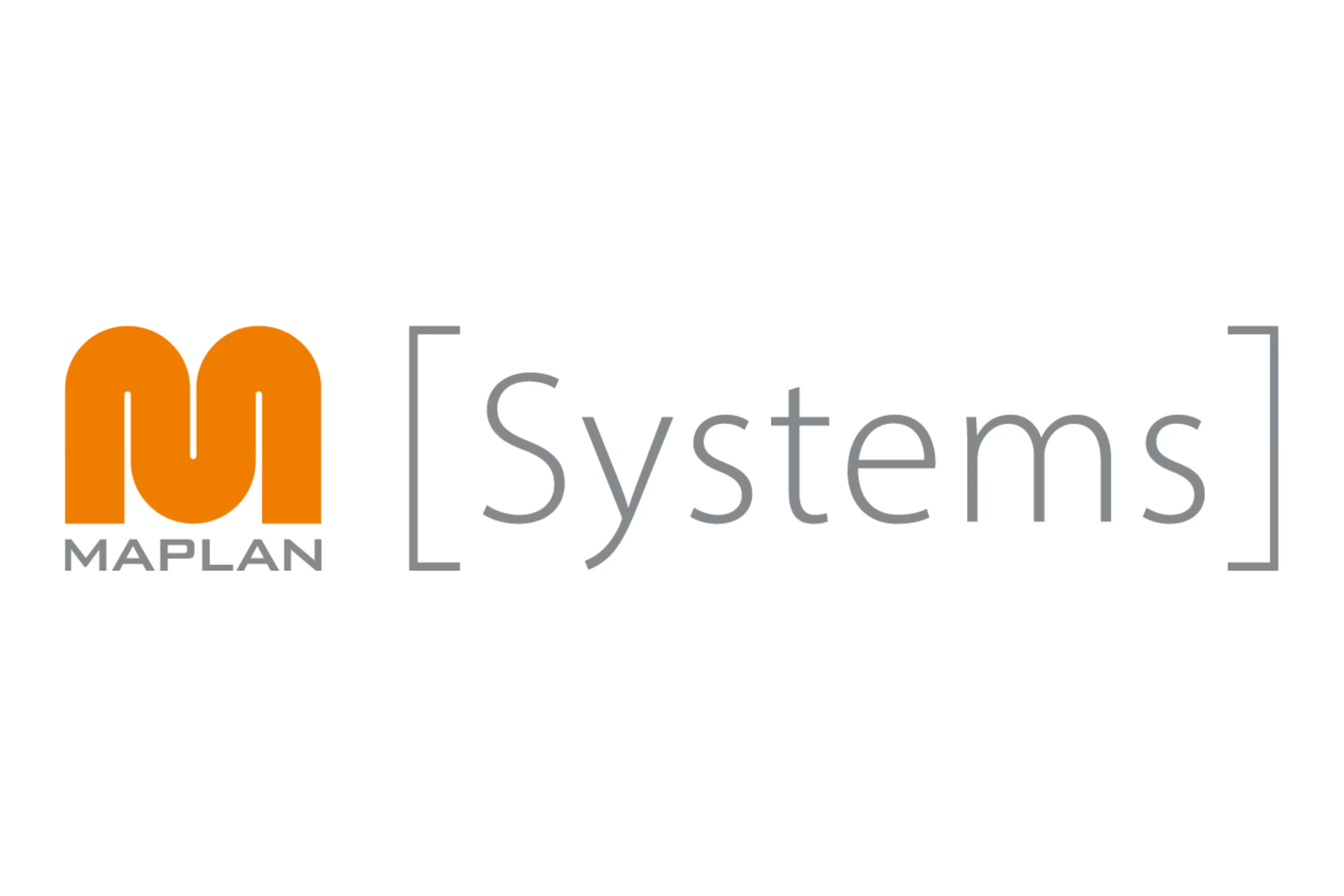
Portrait of the user
MAPLAN is a leading manufacturer of elastomer injection molding machines and offers comprehensive 360° system solutions for the semi-automatic and fully automatic production of rubber and silicone products. As a full-service provider, the company supplies machines, cold runners, molds and turnkey automation systems for customers in the automotive, railroad, energy technology, medical technology and household appliance industries.
In addition to its headquarters in Austria and subsidiaries in the USA, China, India, Germany, France, Italy and Slovakia, MAPLAN is represented globally with more than 20 sales and service locations worldwide.
MAPLAN Systems GmbH, in the south of Germany, is the competence center for the production of precision tools and cold runners.
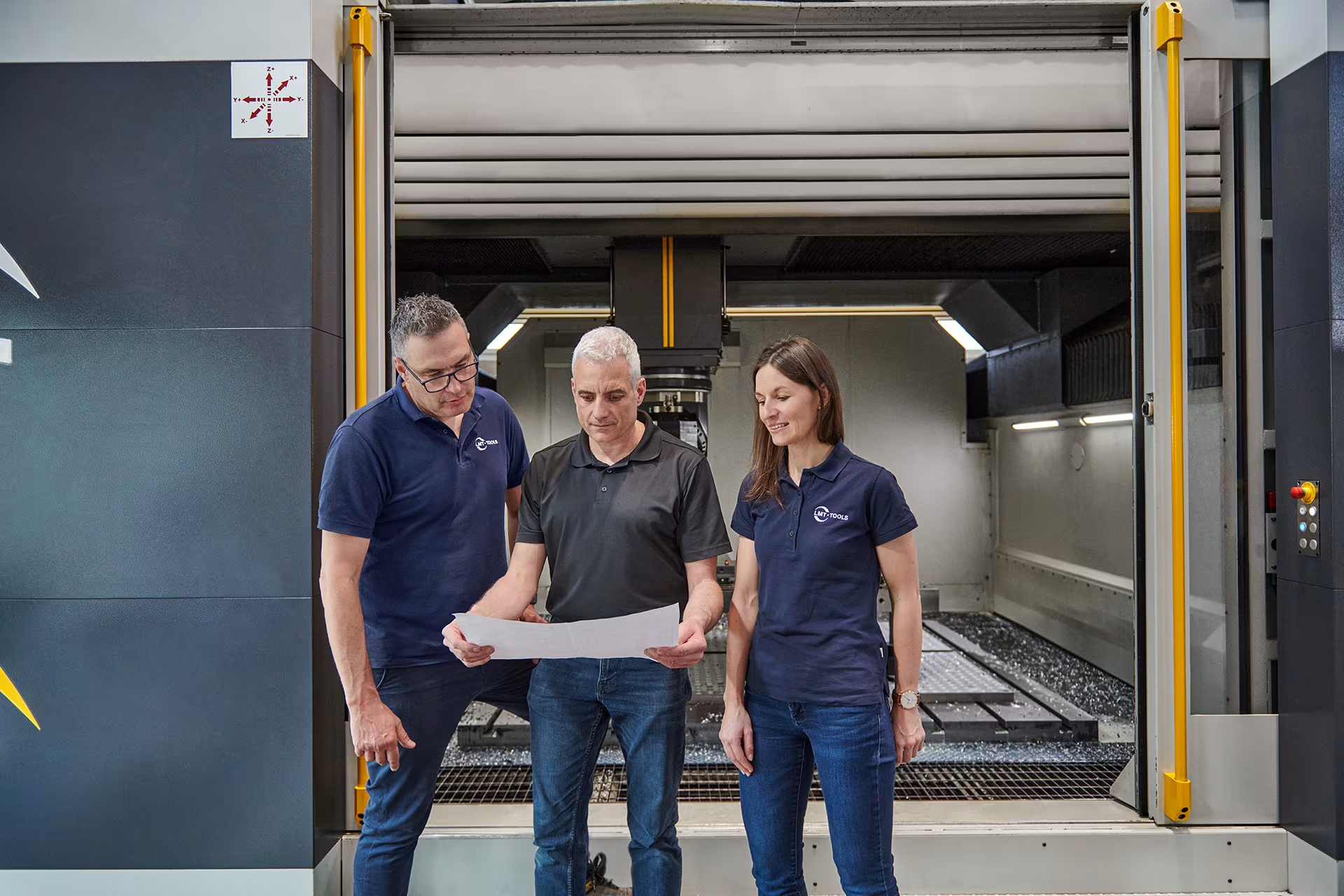
Initial situation: High demands on precision and process reliability in mold making
MAPLAN Systems GmbH in Villingen-Schwenningen specializes in sophisticated single-part production in mould making. In a current project, several components with a high number of threads were to be manufactured in steel, in the material 1.2312 - each with high precision and absolute process reliability. As this was the final processing stage of the workpieces, an error-free and stable process was crucial. At the same time, it was important to optimize the machining times and ensure cost-effective implementation in single-part production.
To meet these challenges, MAPLAN was looking for a reliable partner with comprehensive thread expertise - and found it in LMT Tools. With the modular HPF Max Former from the LMT Fette brand, a solution was implemented that both met the required quality standards and significantly increased production efficiency.
What advantages did Ralph Hug from MAPLAN Systems GmbH see in thread forming and the implementation with the modular HPF Max Former?
As thread cutting is the last machining step in the production process, process reliability was of central importance to Ralph Hug, Operations Manager at MAPLAN Systems GmbH. He deliberately opted for the non-cutting thread forming process.
“I have had very good experiences with LMT Kieninger in die and mold making - both in terms of the quality and performance of the tools as well as the service,” explains Hug. “For this order with recurring threads, it was important for me to have a reliable partner with comprehensive threading expertise at my side. That's why I opted for LMT Fette.”
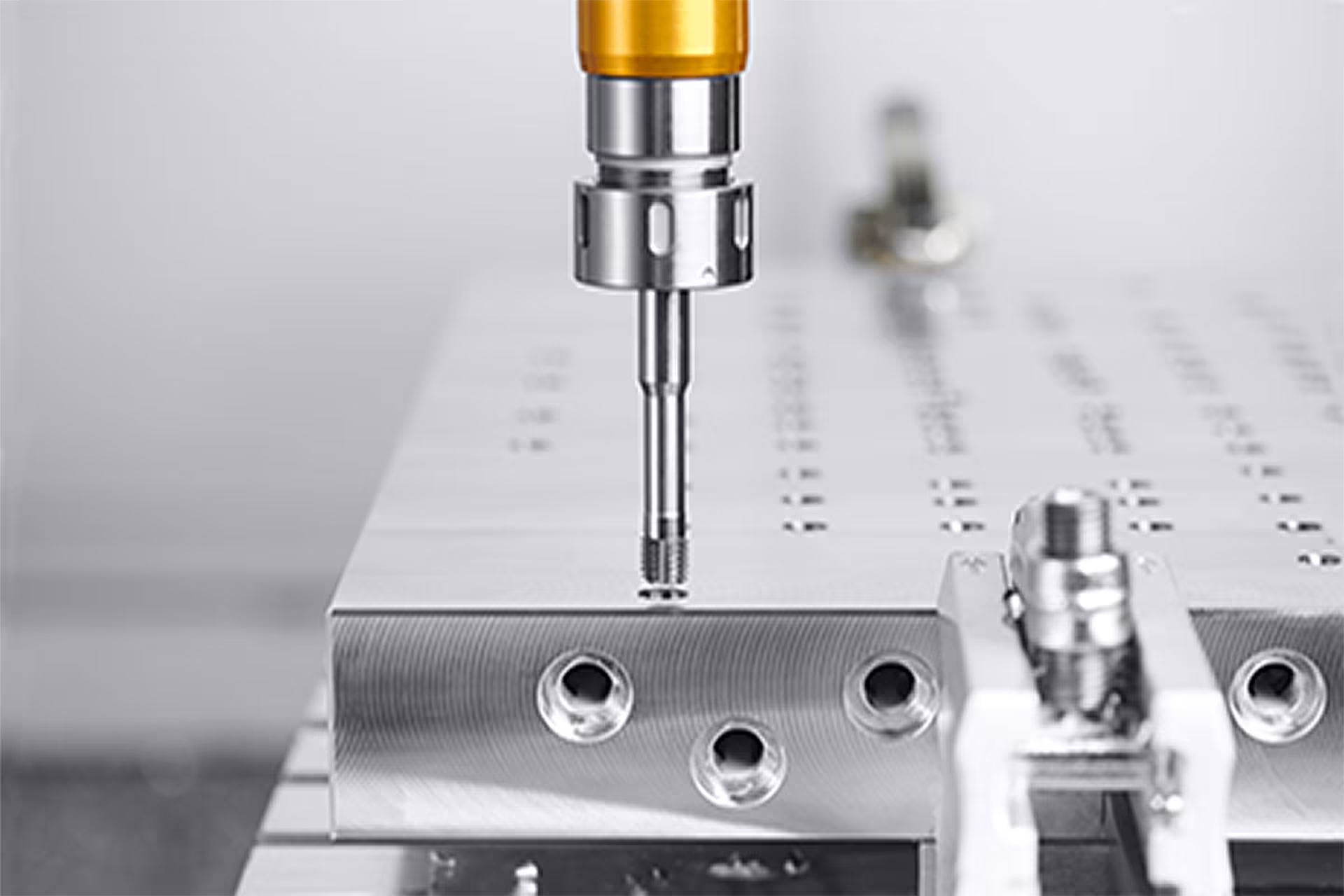
The optimum tool solution: the modular HPF Max thread former
The modular HPF Max Former from LMT Tools combines the wear resistance of a carbide thread head with the toughness of a steel shank - ideal for demanding threading applications. Its high peripheral speed significantly reduces the machining time.
Another advantage: different thread dimensions can be realized with just one tool holder. This significantly reduces both set-up and tool costs. In addition to the extensive standard range, LMT Tools also offers customer-specific special solutions, individually tailored to the respective application.
The result? A significant increase in efficiency and reduced production costs
By using the modular HPF Max former, MAPLAN Systems GmbH was not only able to reduce processing times, but also ensure a high level of process reliability and stable series production - even in unmanned operation.
The bottom line: precision and efficiency combined
The implementation of the HPF Max at MAPLAN Systems GmbH underlines the importance of choosing the right tool for stable, economical and automated thread production.
"With the modular HPF Max former from LMT Tools, we were able to make our production significantly more efficient and at the same time increase the service life of the tools." - Ralph Hug, Operations Manager, MAPLAN Systems GmbH
This project shows: With the right tool, even the most demanding manufacturing tasks can be solved reliably and economically. We would like to thank MAPLAN Systems GmbH for their trust and look forward to further successful projects in the future.
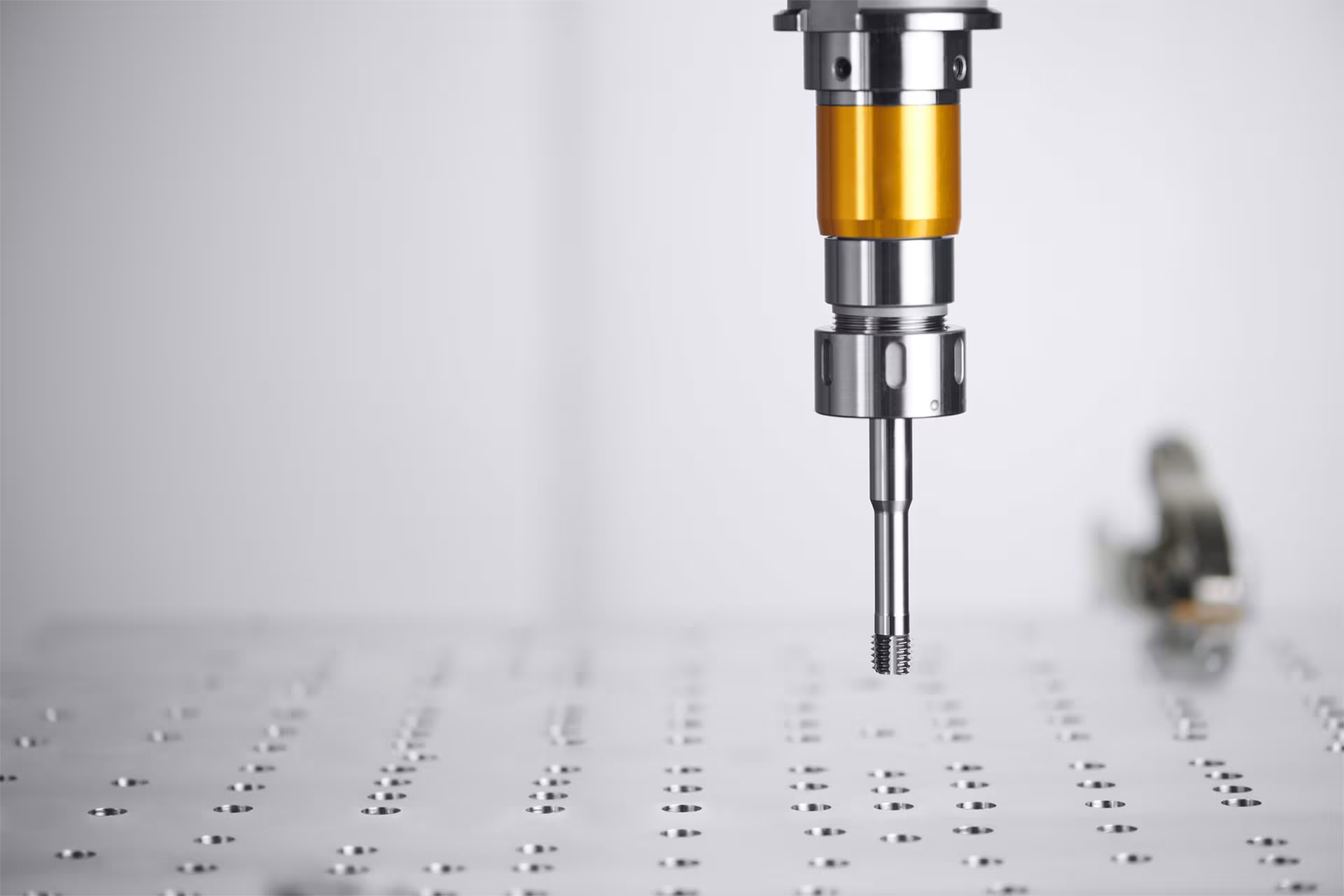
Would you also like to optimize your processes?
Contact our team for individual advice at info@lmt-tools.com or discover the HPF Max directly in the store:
Shop now